A question we get asked a lot in the Ecoboost community is: Are throttle closures at WOT bad? Well, let’s delve a little deeper and see what throttle closures really mean. We’ll first need to dive into a little bit of background knowledge on how the Ecoboost throttle is controlled.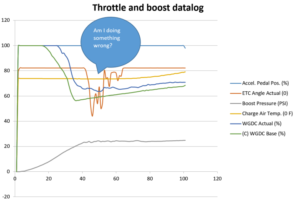
The first important thing to grasp is the concept of Load. Load as defined by Ford is a representation of how much air is filling the cylinder per intake event compared to an ideal amount of air that would fill it at 100*F air temperature and 200*F engine coolant temperature. A load of 1.0 represents that the cylinder has filled with this ideal amount (or in Ford terms “standard”) of air. A load of 2.0 would thus represent twice that amount of air. Another way to think of load is that it represents engine torque output.
By controlling load, we control the amount of air in the cylinder, which directly controls how much fuel we need (for a set AFR), and ultimately the torque the engine produces.
The ECU takes a torque request from the accelerator pedal, applies torque, fueling, and over-temperature limits to it, and ultimately converts that final torque request into a load. These limits can be vital to engine safety and thus the ECU is keen to sticking to its desired loads. This Desired Load is then further converted into a desired air mass.
This air mass then gets worked backwards through a volumetric efficiency model to FINALLY give us a desired manifold absolute pressure (MAP). This pressure can be below atmospheric (vacuum) or above (boost).
So, we have a desired MAP, but most of us know that Ecoboosts have at least two sensors in the intake tract that measure pressure, one in the manifold (measuring MAP), and one pre-throttle (known as the Throttle Inlet Pressure or TIP sensor).
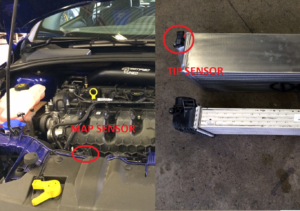
Theoretically, if the throttle wasn’t a restriction, MAP and TIP should be equal at steady state, but with a throttle in the way, even fully open, there’s a slight pressure drop across the throttle. To solve this issue, Ford actually sets a desired TIP value that is slightly above desired MAP. That way if they try to reach a set TIP pressure, they will simultaneously hit their Desired pressure target.
The throttle plate is opened and closed electronically so that whatever TIP you currently have can be adjusted to your desired MAP. At part throttle, TIP is typically atmospheric since there is no vacuum before the throttle plate, so the throttle remains mostly closed to keep your MAP low. At WOT, you will mainly see a throttle plate that is wide open (about 82% on a COBB AP datalog). The throttle plate moves to make sure we hit our desired pressures and loads/torque as set by the calibration/tune. But wait, there is more!
On turbocharged vehicles under high loads the turbocharger is used to pressurize the intake tract to achieve the desired torque we were shooting for. The turbocharger speed and air delivery is controlled by the wastegate, which also receives its inputs from Desired TIP and Desired Airflow. If the throttle is held wide open, it is only up to the wastegate to control how much pressure and airflow we have under boost.
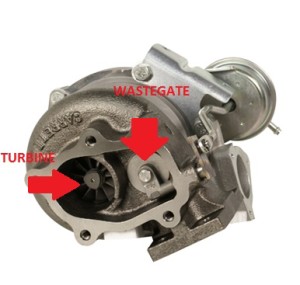
So why then, would we ever want to see a throttle closure at WOT? Typically if you see throttle plate closures under WOT it means your TIP Actual / Airflow Actual ended up higher than what the ECU is asking for. Thus the ECU has to close the throttle to prevent the manifold from getting too much air. As mentioned previously, we may be limiting this for safety, to make sure we have enough fuel, or maybe we even had a component failure (like a wastegate line popping off!) and need the throttle to shut to save us from a costly mistake.
But, that’s not the only case – there is actually a performance benefit to closing the throttle at times and controlling airflow via BOTH the wastegate and throttle. A turbocharger is a mechanical machine that does NOT have instantaneous response. It has an inertia and it takes time to get it to spin up and start compressing air. One of the big things you see discussed is turbo lag or how long it takes to spool. Because we have both the wastegate AND the throttle controlling airflow, we could theoretically pre-spool the turbo a little more than we need at the moment, and use the throttle as a restriction to hold back that extra pressure from the manifold. This has the effect of moving us straight up on a compressor map. We have higher pressure, but the same airflow. The net result is that when we now request the power, we’ve already built up some turbocharger rotational energy and don’t need to spend time building it up! That means a faster response when stepping and requesting that oh-so-sweet turbo induced torque!
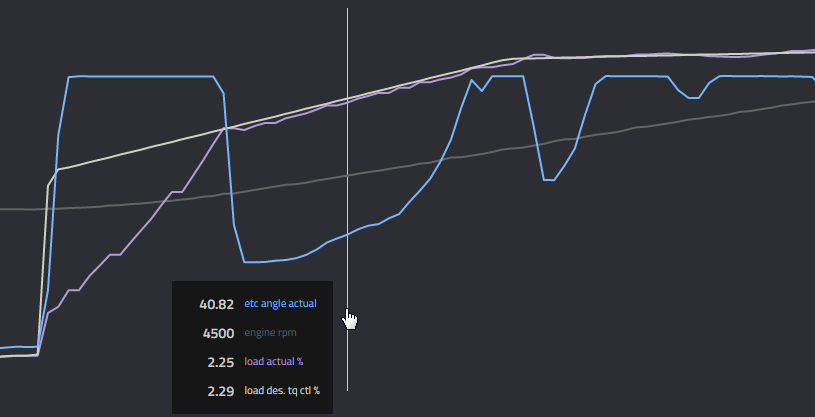
Cut that turbo off! We don’t want more load than we can handle!
This tuning strategy however should not be abused. Keeping the wastegate shut increases pre-turbine pressure, decreases volumetric efficiency, and hurts your fuel economy, so we don’t always want to keep it shut. Like wise, pre-spooling the turbo too much can cause compressor surge. To address this, the ECU controls TIP separate of MAP, which sets a boundary of how much higher we want TIP to be over MAP. As well, the surge line is stored in the ECU and if TIP rises beyond that point, the electronic bypass valve (BPV) can intervene preventing surge. Using this,we can set TIP targets higher in conditions we expect to need acceleration, maximizing performance. This can be a big benefit especially on a road course where you may be part throttle around a sweeper, and once you’re lined up on the straight you can gun it and have a head start on the other cars that take a little longer to spool because they weren’t pre-spooled. However if you see throttle staying consistently at 20-30% for the entire pull, you’re likely dealing with a mechanical or tune issue.
In summary using the throttle smartly when tuning can result in the fastest possible boost response during transient throttle applications while also making sure that boost stays on target. With proper tuning of the system, the wastegate and throttle both allow you to create fast spooling yet smooth and controlled boost. This can be seen on the dyno (or VDyno if you have a clean one without wheelspin!), with nice smooth torque curves lacking any overshoot typical of a poor implementation of mixing throttle and wastegate.
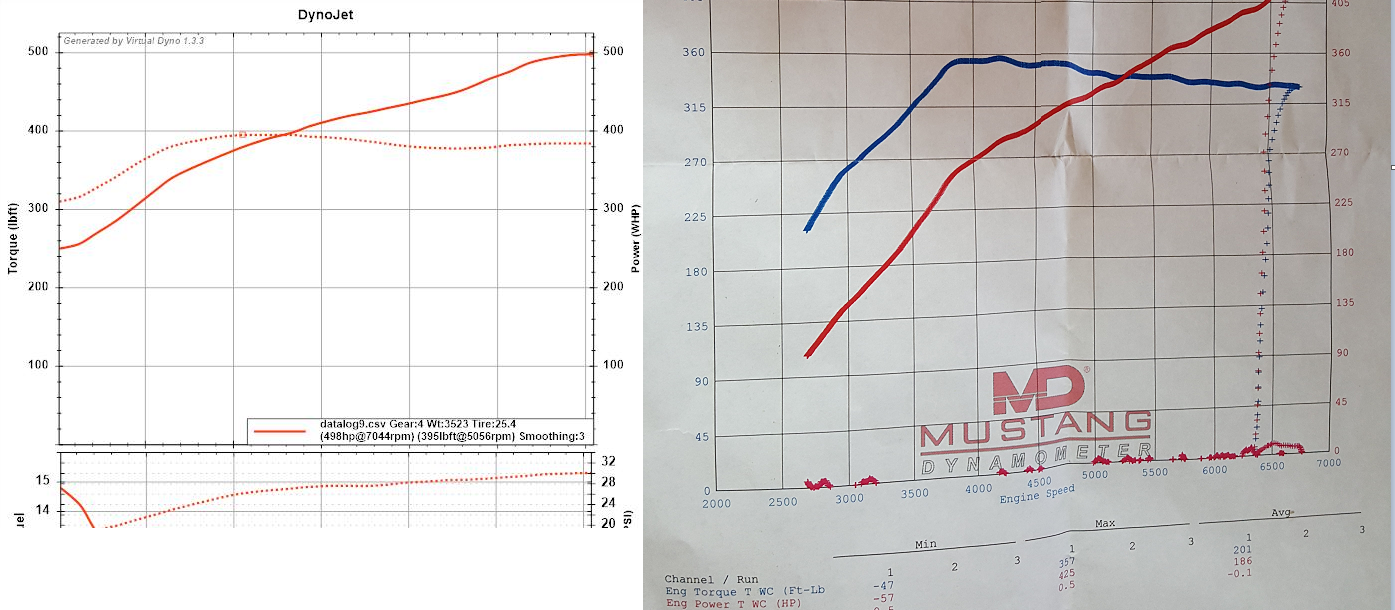
Net result of throttle and wastegate combined: Nice flat torque without overshoot.
So now hopefully it’s clear that having throttle closures isn’t necessarily bad. Quite the opposite – relying on just keeping the throttle open the whole time and using the wastegate only is a step backwards and leaves performance on the table.